When a CNC lathe machine a tapered part, the face of the part needs to be tapered in order to obtain a real part from the model. Before tapering the model, the engineer looks at all faces that need to be tapered and have the same draft definition. CNC lathes support this process. Engineers use different tools to group faces that need to be tapered and have the same draft definition.
WHAT IS TAPER?
Taper refers to the ratio of the diameter of the bottom surface of the cone to the height of the cone. If it is a truncated cone, it is the ratio of the diameter difference between the upper and lower bottom circles to the height of the truncated cone. The taper plug gauge is mainly used to test the major diameter, taper and contact rate of the product, which is a special comprehensive inspection tool. Taper plug gauges can be divided into two types: size plug gauges and coloring plug gauges. Because the design and detection of the painted taper plug gauge are relatively simple, it is widely used in workpiece measurement.
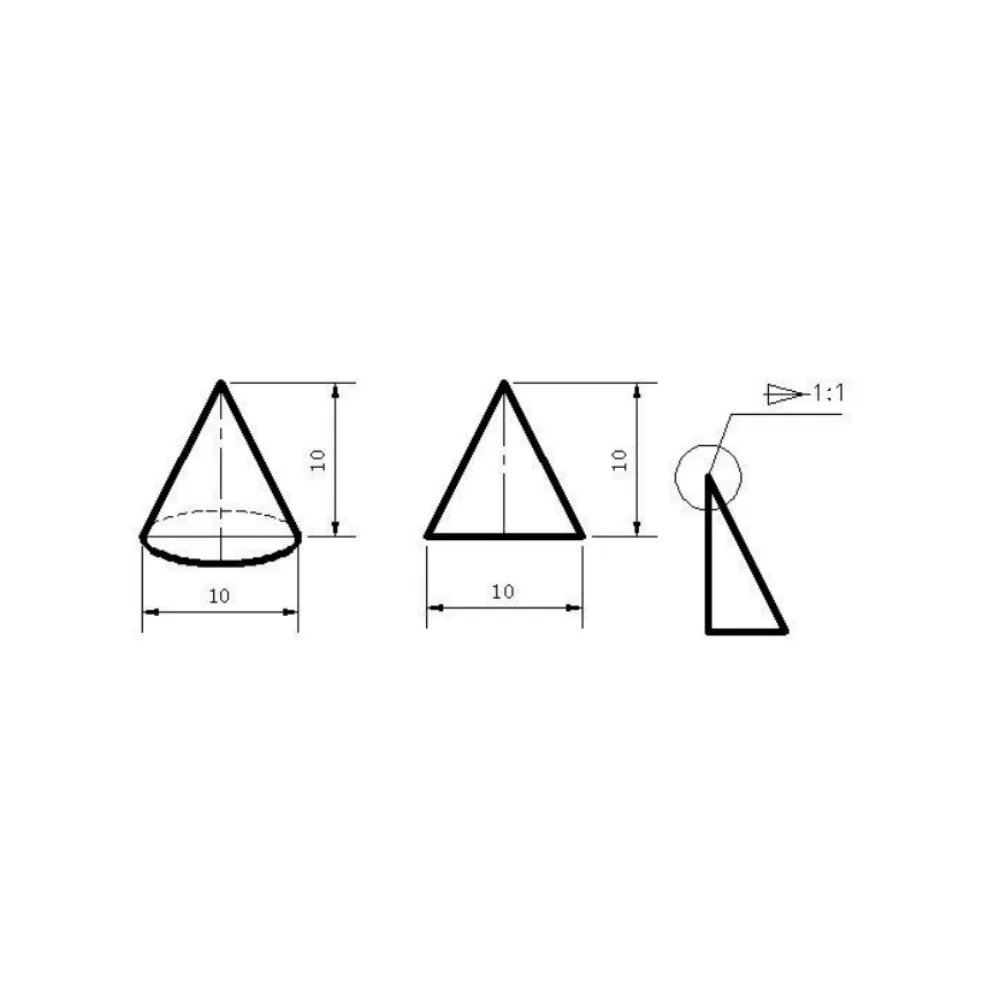
In ordinary linear turning, the tool moves along a straight line parallel to the axis of the workpiece so that the finished workpiece always has the same diameter. However, when cutting a tapered workpiece, the tool is at an angle to the axis of the workpiece, creating a taper. Therefore, to turn a taper, the workpiece must be mounted on the lathe so that the axis of rotation of the workpiece is at an angle to the axis of the lathe, or the tool is moved at an angle to the spindle of the lathe. A piece is said to be tapered when its diameter varies uniformly from one end to the other.
Taper turning as a machining operation is the gradual decrease in diameter from one part of a cylindrical workpiece to another The taper can be either external or internal. If a workpiece is tapered on the outside, it has an external taper; if it is tapered on the inside, it has an internal taper.
HOW TO MACHINING THE TAPER OF THE WORKPIECE ON THE CNC LATHE?
The method used to turn a tapered workpiece depends on the location of the taper (internal or external taper) and length of the workpiece and the number of workpieces to be machined. The three basic methods of turning a taper require the operator to use a forming tool, offset the tailstock, or turn with a taper attachment. With either of these methods, the tool must be precisely centered with the axis of the workpiece, otherwise the workpiece will not be a true cone, and the speed of the cone will vary with each cut. The following mainly explains the method of machining taper workpieces on lathes.
Forming Tool Method. Form turning is one of the simpler taper turning processes in lathes to produce short tapers. This approach is shown in the taper diagram below. Ground the form to the desired angle. As the workpiece rotates, the tool is fed perpendicular to the lathe axis.The length of the turning edge of the lathe taper forming tool must be greater than the length of the taper. Because the entire turning edge removes metal, there is a lot of vibration and therefore a lot of force. It does it slowly.
Offset Tailstock Method: This method works well for small cone angles. The workpiece will be placed between the active center and the active center, and the taper can only be turned between the centers. The tailstock is clamped to the lathe opposite the headstock. In the normal position, the dead point is on the rotary axis, and the movement of the tailstock can be realized by offsetting the screw. When the workpiece is fixed with a live center and a dead center, the rotation axis of the workpiece becomes a straight line at a certain angle to the feed. Turning where the tool is at an angle to the workpiece axis when the tool is fed creates a taper.
Using the Taper Turning Attachment Method: If the length of the tapered workpiece is greater, the taper turning attachment can be used for longer tapers. In this taper turning method of lathe machining technology, the different attachments of the lathe are attached to the rear end of the bed by using a base plate or bracket, the taper turning attachment. It has a guide bar that is usually centered on a pivot. The guide rod has a swing function, and the angle can be set arbitrarily.
On either side, the guide bar can be rotated up to a maximum 10° angle. It has a guide block that is attached to the rear end of the cross slide and moves on a guide rod. Before attaching the cross slides, the set screws are removed, so the cross slides are free from the cross slide screws.
The article mainly introduces how to process the taper of the lathe. After browsing the full text, you can understand that the method used to turn the taper workpiece depends on the taper (inner taper or outer taper) and length of the workpiece, as well as the number of workpieces to be processed. The three basic methods of turning a taper require the operator to use a forming tool, offset the tailstock, or turn with a taper attachment. With either of these methods, the tool must be precisely centered with the axis of the workpiece, otherwise the workpiece will not be a true cone, and the speed of the cone will vary with each cut.