At present, almost all metal shells of mobile phones are processed using CNC machine tools. The method of CNC machining metal case has become the choice of the 3C industry due to its advantages of high efficiency, high precision, and stable processing quality.
The all-metal integrated CNC machining process was first pioneered by Apple – aluminum plates are made of die-casting cylindrical solid aluminum materials, which are precision CNC processed and cut into prototypes of integrated machines. As the body gradually took shape, the shape of the keyboard and various subtle structures on the body were worn off. This process involves a total of nine CNC milling processes, followed by obtaining an accurate overall shell.
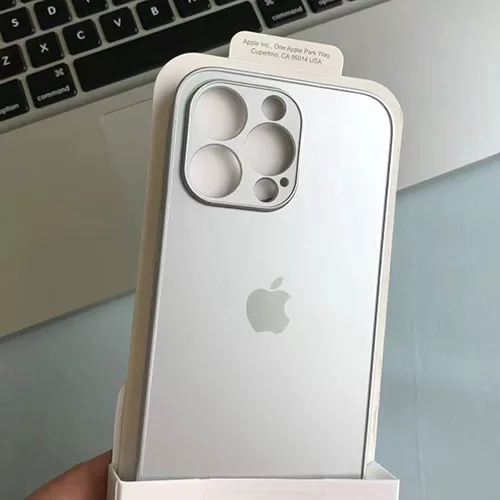
Manufacturing a metal casing for a mobile phone requires multiple processes from programming to obtaining the finished product, including rough machining, semi rough machining, semi precision machining, and precision machining. Often, the entire process requires more than 10 processes to obtain the finished product. To improve the yield rate, strict control is required for each process.

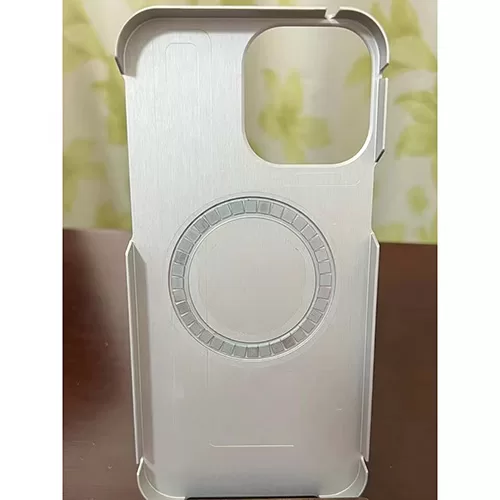
Before starting the CNC machine tool, it is necessary to first model and program the metal phone case. The difficulty of 3D modeling is determined by the structure of metal phone cases. Modeling metal phone cases with complex structures is more difficult and requires more and more complex programming processes. Programming includes process settings for machining, tool selection, speed settings, and the distance of each tool feed. In addition, different products have different clamping methods, and fixtures need to be designed before processing. Some structurally complex products require specialized fixtures.
Programming includes the processing technology of the entire metal phone case. Although CNC automation is used to complete the subsequent steps, experienced personnel must be involved in the early stages of programming to avoid multiple trial and error and increase costs.
Use a high-speed drilling center to accurately mill the aluminum sheet into a regular three-dimensional volume of a certain size, and prepare for the next processing step. Rough milling: After positioning, rough milling is carried out to remove the internal cavity structure, positioning columns combined with fixtures, and most of the external redundant materials. Milling antenna slots: The signal problem with the all metal shell is very tricky, and it is necessary to mill out antenna slots to leave a transmission path for the signal and maintain necessary connection points to ensure the strength and overall sense of the body. CNC precision machining: precision milling of inner cavity, outer structure, outer surface, side edges, etc. Polishing: Use high-speed and precision CNC machine tools for polishing, eliminate knife marks, and prepare for subsequent sandblasting. Sandblasting: To treat the metal surface to a matte finish.